About Plate Heat Exchanger - Gasket
Incompressibility The rubber compound can change shape after being squeezed it will return to original vulcanized shape.
Strength It is strong enough for withstand the forces normally incurred by squeezing into position and being acted upon by pressurized liquid.
Softness The rubber is strong enough for the application but still soft enough for conform closely to the metal surfaces and provides a seal without undue stresses being applied.
Resistance to Temperature All polymers will only behave as a rubber over a relatively short range of temperature. Thus careful selection of the compound according to the required temperature range is necessary.
Longevity Synthetic polymers have a built in superiority in terms of useful lifetime, and modern additives can further enhance this property. It is in this area that the correct compound selection is of vital importance.
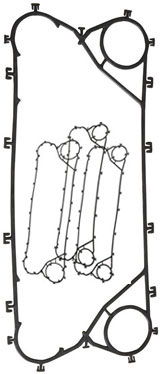
Plate Heat Exchanger Gaskets
All plate heat exchanger gaskets are manufactured in accordance with a rigorous quality control procedure. With our gasket testing facilities, we are able to fully inspect gaskets to ensure they continuously meet our high standards.
For this reason, we are able to offer a 12 month warranty (subject to conditions) on all plate heat exchanger gaskets supplied by us.
Depending on the heat exchanger manufacturer and model type the heat exchanger gaskets are fixed to the heat transfer plates either mechanically or with an adhesive.
The common attachments are listed below. For more detailed information select a specific manufacturer.
Adhesive Attachment
With adhesive attachments a “glue” is used to bond the heat exchanger gaskets to the heat transfer plates. The adhesive does not contribute to sealing the heat exchanger it is merely used to hold the gasket in place while the heat exchanger is tightened – it is the tightening down of the heat exchanger which compresses the plate/gaskets and creates the seal.
- Pros. The gaskets remain attached to plates when being cleaned on site. i.e. when using a high pressure washer.
- Cons. When replacing gaskets the heat transfer plates require off site servicing to ensure the gasket grooves are clean and the new gaskets are bonded correctly.
Types of attachments.
|
![]() |
Mechanical Attachment
Most modern plate heat exchangers use a form of mechanical attachment to fix the gaskets to the heat transfer plates.
- Pros. The gaskets can be easily removed and replaced, especially on site, as the gasket sealing area remains clean (free from glue residue).
- Cons. The gaskets will become detached from the heat transfer plates when pressure washing on site or through incorrect / rough handling. Care must be taken when tightening the heat exchanger to ensure the gaskets remain in the gasket groove – occassional checks should be made whilst tightening down so any gaskets that have moved out of the groove can be pushed back in.
Types of attachments.
|
![]() |
|
![]() |
|
![]() |
Elastomers
- NBR(Nitrile)
NBR Operation up to 1000C
NBR High temperature Operation up to 1000C
Their specific features are their remarkable resistance to oils, solvents and grease, wheather aliphatic or aromatic.
- HNBR (Nitrile Hydrogene)
HNBR* Operation up to 1500C
Its physical properties are remarkable even at high temperatures.
Good behaviour at low temperatures.
Good resistance to numerous chemically aggressive oils.
*THERBAN. Bayer registered trade mark
- EPDM
EPDM Operation up to 1400C
Excellent resistance to all kinds of ageing (heat, oxygen, ozone, weathering).
Sensitive to ultraviolet radiation and light.
Good chemical resistance to ketones, alcohols, and diluted bases together with certain lubricants (Lockheed, Skydrol).
Very low resistance to hydrocarbon solvents and oils.
- IIR (Butyl)
IIR Operation up to 1600C
Butyl rubber vulcanates have excellent thermal, chemical and mechanical stability.
They age very well when exposed to ozone and heat.
Very good resistance to acids and bases at average levels of concentration and to polar solvents and animal or vegetable oil.
- FPM (Fluorocarbone)
FPM* Operation up to 2500C
High resistance to extreme temperatures: -500C to +2500C.
Resistance to most fluids or industrial use.
Resistance to thermal cycles.
*Type A VITON, Dupont Dow Elastomers registered trade mark.
FPM* type vapeur Utilisation jusqu’a 2750C
The vulconisates keep their technical characteristics better than standard FPM after heat exposure ageing
*Type B VITON. Dupont Dow Elastomers registered trade mark.
FPM* haute performance Utilisation jusqu’a 2500C
High resistance to extreme temperature: -500C to +2500C.
Optimum resistance to chemical product.
*Type G VITON. Dupont Dow Elastomers registered trade mark.